Progressing Cavity Pumps: Key Features & Applications
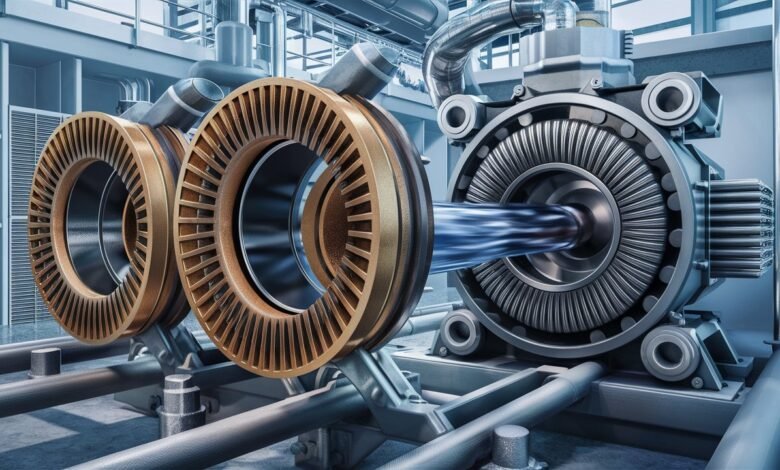
Introduction
Discover how progressing cavity pumps operate and how this technology transforms fluid handling. Spec pumps are very particular and useful in many fields of operation in different industries. Go over their particulars to get to the root of their performance.
A Progressing cavity pump which can also be called a progressive cavity pump or an eccentric screw pump employs a helical rotor and stator. It offers a steady and accurate flow of the fluids, and therefore, makes it the most suitable design when dealing with thick or sensitive fluids.
Suitable for both high and low pressure uses, these pumps are considered to have very low pulse flow, making them extremely efficient. Studying these elements and their applications will reveal why they serve in complex fluid operations.
How Progressing Cavity Pumps Work
Progressing cavity pumps use a helical rotor contained in a stator with twice the helical turns, functioning as positive displacement pumps. This is an inducement technique as the rotor turns it produces a series of sealed chambers that transport the fluid in the pump. It is possible to note the movements of cavities of the fixed size all the time, which guarantee pulsation-free continuous flow. Due to the design of the pump it can transport thick slug and grievous chemicals and liquids without excessive shear and disturbing their nature.
Applications across Industries
Industries apply progressing cavity pumps in various areas, such as the food industry, edible oil and oil seed production, and water treatment. Due to their incapability of working with some fluids like viscous, abrasive, or shear-sensitive, requirements of the pumps such as pumping of the sewage, coal slurry, and whole mud in the directional drilling, etc. This guarantees that they meet the specialized requirements of multifaceted industrial processing.
Design Variations and Their Impact
Pc pump designs can differ in many parameters; this affects their efficiency and applicability to related operations. These following stators are some of the most used; the equal-walled stators and the different-walled stators. To be used under high precision and for long lasting use, the stators should be equal-walled but if the manufacturing plant wants to handle large solid materials it has to use unequal-walled stators. These designs impact properties such as pressure holding capacity, flow rate, and the material’s ability to withstand wear and tear.
Maintenance and Operational Considerations
Maintenance is an essential aspect in the operation of progressing cavity pumps given its positive impact on the pumps’ durability and effectiveness. These pumps need proper lubrication and the failure to produce this fluid affects the working of this pump by making it to deteriorate at a very fast pace. Failure and wear of the stator and rotor components demand their regular replacement or acquisition of new ones in order to avoid hitches.
Historical Background and Development
The application of the progressing cavity pump was first introduced in 1930 by René Moineau. Moineau successfully created the first of its kind as a compressor for jet engines and soon found its way to a pump design improving the overall fluid management. His prodigious work had made him build the model for today’s progressing cavity pump.
Choosing the Right Pump for Your Needs
Choosing the right progressing cavity pump means and depends on the needs of the certain application. Issues like the type of liquid that is to be pumped, possible pressures involved, and if there are any solid contents should be considerations in this regard. Consult professionals and assess technical aspects to ensure you meet your operational needs when selecting a pump.
FAQ’s
What is a progressing cavity pump?
A progressing cavity pump is a positive displacement pump that moves fluid through fixed-size cavities formed by a rotating helical rotor.
What are the main applications of progressing cavity pumps?
Industries use them for food and beverage processing, oil extraction, wastewater treatment, and pumping viscous or shear-sensitive fluids.
How does a progressing cavity pump differ from other pumps?
Unlike centrifugal pumps, progressing cavity pumps provide a steady, pulse-free flow and handle high-viscosity fluids effectively.
What maintenance do progressing cavity pumps require?
Regularly lubricate the pump and avoid running it dry; monitor and replace parts like the rotor and stator as needed.
Who invented the progressing cavity pump?
René Moineau developed the progressing cavity pump in 1930, initially as a compressor for jet engines.
Conclusion
Many industries consider progressing cavity pumps appropriate tools due to their special features, such as their suitability for pumping viscous and shear-sensitive fluids. They come in a helical rotor and stator type, and the swirling flow and low pulsations would make these pumps suitable for intricate duties. The jet engine compressors were earlier used to make these pumps and hence, traces their history as multifunctional fluid handling possibilities. Thus, it is crucial to comprehend their functionality and requirements for effective application in industrial applications.